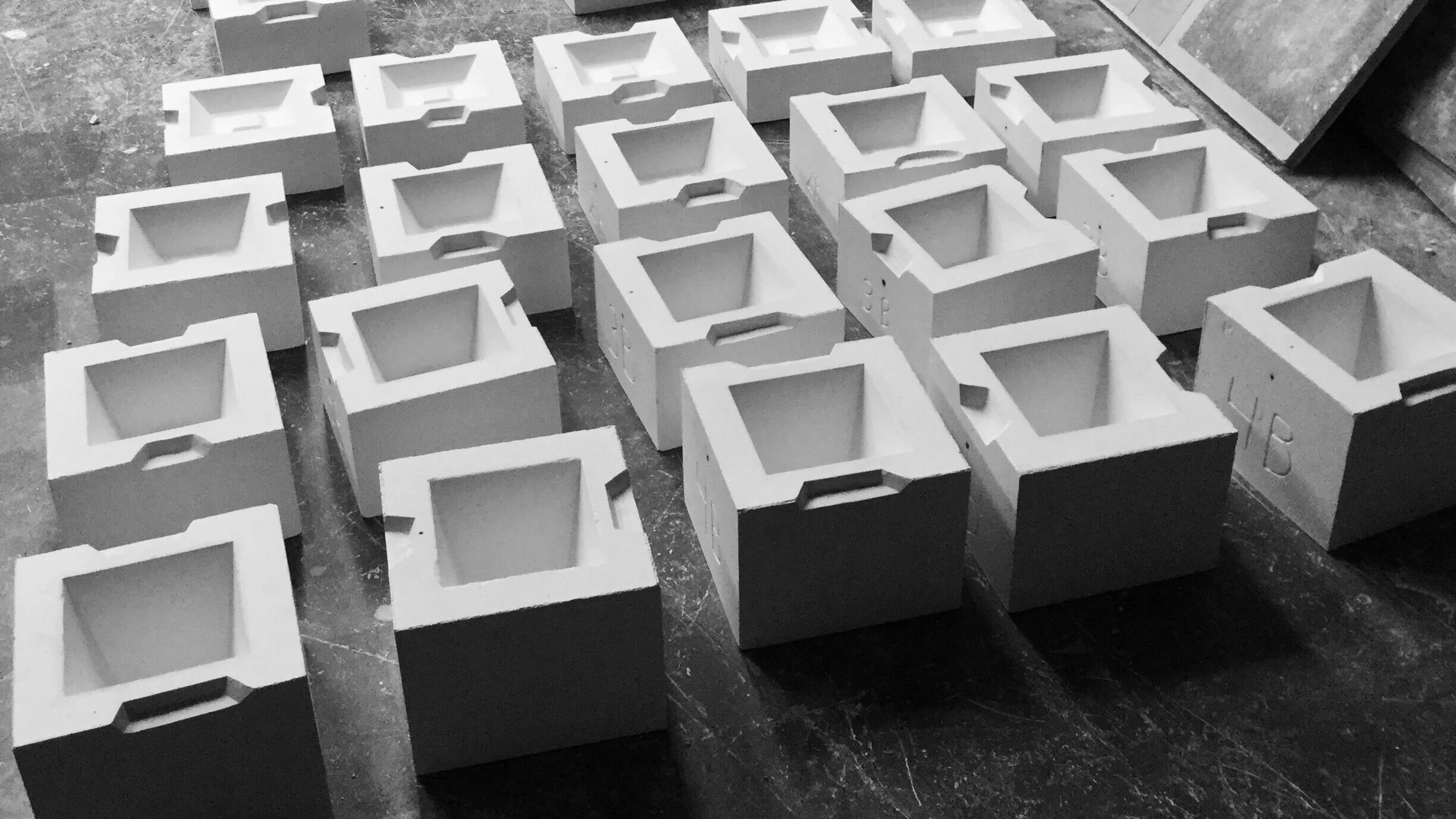
Mould making is central to my creative process.
It is a labour intensive craft ideal for producing asymmetrical and sculptural forms.
Mould making delivers refined ceramics with precise detail, and opens up limitless possibilities in surface design and colour treatment.
I begin by sculpting a model in clay. In the early stages I am focused on capturing a form with bold gestures and in understanding the dynamic relationship between its parts. I make a quick waste mould of the clay model and reproduce it in plaster, a firmer material that permits me to refine the surface.
Once the form of the model is resolved I make a complex mould in multiple parts for slipcasting in ceramic. For the process of slipcasting, a liquid clay body (slip) is poured into a plaster mould that absorbs water out of the slip, causing a layer or cast to form on the mould’s interior that will become the finished work.
The surfaces of my ceramics are made with layers of coloured porcelain slip applied directly into the mould. Through slipcasting with colour, I push to reinvent a work with every casting. I constantly experiment with new colour combinations and methods of application to give each work a unique identity. I employ this method over traditional glazing for the intensity of colour I can achieve and for the way colour hugs the surface of each work like a skin.
All works are glazed on the interior so they are water and food safe. The exteriors are left unglazed and sanded smooth to the touch.